NCC 2022 Volume One - Building Code of Australia Class 2 to 9 buildings
Filter
F1
Part F1 Surface water management, rising damp and external waterproofing
Part F1 Surface water management, rising damp and external waterproofing
Introduction to this Part
This Part is intended to minimise the risk of water leaking into or accumulating within a building and causing unhealthy conditions or damaging building elements by corrosion or rot. It is also intended to prevent water redirected away from the building damaging nearby properties.
Objectives
F1O1
Objective
2019: FO1
F1O1
Objective
2019: FO1
The Objective of this Part is to—
- safeguard occupants from illness or injury and protect the building from damage caused by—
- surface water; and
- external moisture entering a building; and
- the accumulation of internal moisture in a building; and
- protect other property from damage caused by redirected surface water.
Safeguard occupants and protect the building—F1O1(a)
F1O1(a) aims to minimise the risk of water leaking into or accumulating within a building and causing musty, damp and unhealthy conditions or damaging building elements by corrosion.
Examples
F1O1(a) aims to minimisethe risk of water leakinginto or accumulating within a buildingand causing musty,damp and unhealthy conditions or damaging building elements by corrosion.
- Damp conditions in houses can cause seriousdiseases. What appearto be less serious illnesses, such as colds, can have serious consequences, particularly for children and the elderly.
- Rotten floorboards can collapse, causinginjury.
- Electrical connections can corrode, causingfailure of safetydevices, or increasing the risk of electrocution.
- Penetration of moisture into building elementscan cause degradation to a buildinglong before the damage is detected.
Protect other property from damage—F1O1(b)
F1O1(b) aims to minimise the risk of other property being damaged by surface water redirected from a building or any associated sitework. Property that is to be protected from redirected surface water includes buildings on the same allotment, buildings on adjoining allotments, adjoining allotments themselves and roads.
Examples
Construction on an allotment must not cause re-directed water damage to “other property”, including:
- any building on the same allotment;
- any buildingon an adjoining allotment;
- any adjoiningallotment (whether thereis a building on it or not); and
- any road.
Functional Statements
F1F1
Protection from redirected surface water
2019: FF1.1
F1F1
Protection from redirected surface water
2019: FF1.1
A building, including any associated sitework, is to be constructed in a way that protects people and other property from the adverse effects of redirected surface water.
F1F1 Protection from redirected surface water
People and other property are to be protected from any problems caused by surface water re-directed by a building and any sitework involved in its construction. Remedial works must be undertaken to dispose of any surface water which, because of any variation or addition to its flow caused by any buildingor sitework, causesharm to peopleor other property.
F1F2
Resistance to rain, surface water and ground water
2019: FF1.2
F1F2
Resistance to rain, surface water and ground water
2019: FF1.2
A building is to be constructed to provide resistance to moisture penetrating from the outside, including rising from the ground.
F1F2 Resistance to rain, surface water and ground water
A building must resist:
- rainwater, coming throughthe roof or walls, due to poor waterproofing
- surface water, comingthrough openings which are too low; and
- ground water, which could rise up throughporous floors or walls.
Ground water could enter a building if there are inadequate damp-proof courses or vapour barriers installed, or if other ways of resisting the rising damp have not been provided.
Performance Requirements
F1P1
Managing rainwater impact on adjoining properties
2019: FP1.1
F1P1
Managing rainwater impact on adjoining properties
2019: FP1.1
Surface water, resulting from a storm having an annual exceedance probability of 5% and which is collected or concentrated by a building or sitework, must be disposed of in a way that avoids the likelihood of damage or nuisance to any other property.
Surface water with an annual exceedance probability of 5%
Surface water resulting from a storm with a 5% annual exceedance probability (i.e. a 1 in 20 year storm) that is collected or concentrated by a building or sitework must be disposed of without damage to other property.
Construction should not cause stormwater problems on other properties, worse than those which existedpreviously.
Examples
As a generalrule, undeveloped land tends to absorb rainwater, usually resulting in comparatively slow run-off.
However, a building’s hard surfaces, such as roofsand pavements, causecomparatively quick run-off.Consequently, the design of the surface water disposal system must make provision for run-off stormwater from hard surfaces collected or concentrated by a building or sitework.
Why an annual exceedance probability of 5% for storms?
This is considered an appropriate limit, fair on the person responsible for the building and siteworks and the person responsible for properties affected by re-directed surface water.
F1P2
Preventing rainwater from entering buildings
2019: FP1.2
F1P2
Preventing rainwater from entering buildings
2019: FP1.2
Surface water, resulting from a storm having an annual exceedance probability of 1%, must not enter the building.
Limitations
F1P2 does not apply to—
- a Class 7 or 8 building where in the particular case there is no necessity for compliance; or
- a garage, tool shed, sanitary compartment, or the like, forming part of a building used for other purposes; or
- an open spectator stand or open-deck carpark.
Surface water with an annual exceedance probability of 1%
Building and siteworksmust be arrangedso that surfacewater from a storm with an annual exceedance probability of 1% (i.e. a 1 in 100 year storm) does not enter into a building.
Why an annual exceedance probability of 1%?
A storm with an annual exceedance probability of 5% (1 in 20 year storm) has a less intense flow of water than a storm with an annual exceedance probability of 1% (1 in 100 year storm), which is what the subject building must be protected from.
It is considered more important to prevent water entering a building than it is to prevent water entering a neighbouring allotment or property.
Limitations
The limitations contain several exemptions to F1P2 These are based on the belief that the use and safety levels of the exempted buildings will not be significantly diminished by surface water entering them.
Limitation (a) regarding Class 7 and Class 8 buildings refers only to such buildings which, in a particular case, do not exhibit any need for compliance with F1P2. Such buildings must be considered on a case-by-case basis. However, it is the responsibility of a building proponent to satisfy the appropriate authority that the exemption should apply. The structures like garages, tool sheds, and sanitary compartments forming part of a building used for other purposes are also exempted, provided they do not contribute to the weatherproofing of another part of a building that needs to be weatherproofed. Lastly, open spectator stands and open-deck carparks are not required to comply with this provisions.
F1P3
Rainwater drainage systems
2019: FP1.3
F1P3
Rainwater drainage systems
2019: FP1.3
A drainage system for the disposal of surface water resulting from a storm having an annual exceedance probability of—
- 5% must—
- convey surface water to an appropriate outfall; and
- avoid surface water damaging the building; and
- 1% must avoid the entry of surface water into a building.
Outfall, water entrance and water damage
Under F1P3(a) a drainagesystem for the disposal of surface waterfrom storm with an annual exceedance probability of 5% must:
- have an appropriate outfall; and
- avoid damage to the building.
An outfall includes a kerb and channel, a soakage system, and a natural watercourse, with the decision as to what is appropriate being made by the appropriate authority. Damage to the building could be caused by a building’s subsidence.
Under F1P3(b), a drainage systemfor the disposalof surface watermust avoid surfacewater from a storm with an annual exceedance probability of 1% from entering a building. This provision is intended to prevent surface water causing internal damage to a building, or causing injury or illness to occupants.
The F1P3(b) prohibition on surfacewater entering the building:
- does not prohibita drainage systemthat passes surfacewater through a building (probably by way of pipes) without causing damage; and
clearly does not prohibit water entering a building when it is required for various purposes.
F1P4
Rising damp
2019: FP1.5
F1P4
Rising damp
2019: FP1.5
NCC Blurbs
- undue dampness or deterioration of building elements; and
- unhealthy or dangerous conditions, or loss of amenity for occupants.
- high resistance to moisture penetration; and
- high resistance to damage during construction; and
- high resistance to degradation by dissolved salts.
NCC Title
Rising damp
NCC State
SA
NCC Variation Type
Replacement
NCC SPTC Current
Rising damp
Building Classes
1a,1b,10a,10b,10c
Moisture from the ground must be prevented from causing—
- undue dampness or deterioration of building elements; and
- unhealthy or dangerous conditions, or loss of amenity for occupants.
Limitations
F1P4 does not apply to—
- a Class 7 or 8 building where in the particular case there is no necessity for compliance; or
- a garage, tool shed, sanitary compartment, or the like, forming part of a building used for other purposes; or
- an open spectator stand or open-deck carpark.
F1P4 Rising damp
Building elements must be protected from deterioration and occupants must be protected from unhealthy or dangerous conditions or a loss of amenity causedby moisture from the ground (causing such problems as rot, rising damp, rust, and so on). In essence, this requires that the materials and components which make up building elements must either be fit for this purpose or made fit by protection.
See commentary from F1P2 limitations as the same limitations apply to F1P4.
Examples
The followingmay be acceptable to achievecompliance with F1P4. They should not be regarded as absolute.
- damp-proof course in masonry walls above finished ground level;
- vapour barrier under a concrete slab;
- adequate subfloor ventilation;
- painted or other similar protective coatings on steel and timber on or near ground level;
- appropriate concrete cover on steel reinforcing;
- galvanised coatings on steel; and
specific concrete mixes to achieve required protection levels.
Deemed-to-Satisfy Provisions
F1D1
Deemed-to-Satisfy Provisions
2019: F1.0
F1D1
Deemed-to-Satisfy Provisions
2019: F1.0
SA F1D1 Deemed-to-Satisfy Provisions2019: F1.0
Delete subclause F1D1(1) and insert F1D1(1) as follows:
To clarify that the requirements of F1P1 to F1P4 will be satisfied if compliance is achieved with F1D2 to F1D8.
F1D2
Application of Part
New for 2022
F1D2
Application of Part
New for 2022
F1D2 Application of Part
F1D2 clarifies that F1D4 and F1D5 are not applicable to roofs that comply with F3D2(a) to (d). Additionally, F1D3 to F1D5 do not apply to balconies, podiums, or similar horizontal surface part of a building if the flooring consists of timber decking or other perforated material, or if the structure is located directly above ground.
F1D3
Stormwater drainage
2019: F1.1
F1D3
Stormwater drainage
2019: F1.1
Stormwater drainage must be designed and constructed in accordance with AS/NZS 3500.3.
Explanatory information
Where stormwater drainage does not comply with F1D3, a Performance Solution is to be used to demonstrate compliance with the relevant Performance Requirements.
Requires compliance with AS/NZS 3500.3to achieve compliance with the Performance Requirements.
F1D4
Exposed joints
New for 2022
F1D4
Exposed joints
New for 2022
Exposed joints in the drainage surface on a roof, balcony, podium or similar horizontal surface part of a building must—
- be protected in accordance with Section 2.9 of AS 4654.2; and
- not be located beneath or run through a planter box, water feature or similar part of the building.
Notes
For the purposes of F1D4, an exposed joint is a construction joint, control joint, expansion joint, contraction joint or movement joint and includes an exposed joint which is directly below a drainage surface.
Explanatory information: Location of exposed joints
To minimise the potential of water ingress, the exposed joint should be located at a ridge or high point of the structural substrate, where possible.
Explanatory information: Exposed joints subject to excessive movement
Where an exposed joint is subject to excessive movement, such as more than 10 mm, additional measures should be considered to ensure protection of the exposed joint. These additional measures may include use of a hob with a minimum height of 50 mm formed within the structural substrate for the full length of both sides of the exposed joint, and the exposed joint protected by a discontinuous membrane in accordance with Section 2.9 of AS 4654.2.
F1D4 Exposed joints
F1D4 sets standards for exposed joints in the drainage surface on roofs, balconies, and similar horizontal surfaces. For the purposes of F1D4, an exposed joint is a construction joint, control joint, expansion joint, contraction joint or movement joint and includes an exposed joint which is directly below a drainage surface.
These joints must be protected as per Section 2.9 of AS 4654.2 and must not be positioned beneath or run through planter boxes or water features. The provision aims to minimise water ingress, suggesting joints be located at structural high points when possible. If joints are subject to excessive movement (over 10 mm), additional measures like a hob or discontinuous membrane in accordance with Section 2.9 of AS 4654.2 are recommended.
F1D5
External waterproofing membranes
2019: F1.4
F1D5
External waterproofing membranes
2019: F1.4
A roof, balcony, podium or similar horizontal surface part of a building must be provided with a waterproofing membrane—
- consisting of materials complying with AS 4654.1; and
- designed and installed in accordance with AS 4654.2.
F1D5 External waterproofing membranes
F1D5 referencesthe standard for materials and the design and installation of waterproofing membranes for a roof, balcony, podium or similar horizontal surface part of a building.
F1D6
Damp-proofing
2019: F1.9
F1D6
Damp-proofing
2019: F1.9
- the lowest floor timbers and the walls above the lowest floor joists; and
- the walls above the damp-proof course; and
- the underside of a suspended floor constructed of a material other than timber, and the supporting beams or girders.
- a material that complies with AS/NZS 2904; or
- impervious sheet material in accordance with AS 3660.1.
SA F1D6 Damp-proofing2019: F1.9
Delete subclause F1D6(2) and insert F1D6(2) as follows:
- embossed black polyethylene film meeting the requirements of clause 7.6 of AS/NZS 2904; or
- polyethylene coated aluminium meeting the requirements of clause 7.4 of AS/NZS 2904; or
- bitumen impregnated materials of not less than 2.5 mm thickness, meeting the requirements of clause 7.5 of AS/NZS 2904, when used in walls not higher than 7.8 m above the level of the damp-proof course.
- A Class 7 or 8 building where in the particular case there is no necessity for compliance.
- A garage, tool shed, sanitary compartment, or the like, forming part of a building used for other purposes.
- An open spectator stand or open-deck carpark.
To prevent water penetration of roofs which could cause unhealthy and dangerous conditions or loss of amenity for occupants or dampness and deterioration of building elements.
Damp must not rise from the ground — F1D6(1)
Damp must be preventedfrom reaching:
- a building’s lowest floor timbers;
- suspended concrete floorsor other suspended floors;
- supporting beams or girders; and
- walls above damp-proof courses.
Damp-proof course — AS/NZS 2904 or AS 3660.1 — F1D6(2)
AS/NZS 2904 and AS 3660.1 are referenced as alternative options for damp-proof course materials and installation details.
Exemptions — F1D6(3)
F1D6(3) contains exemptions to F1D6(1) because the safety level of buildings will not be significantly diminished by moisture from the ground.
F1D6(3)(a) regarding Class 7 and Class8 buildings refers only to such buildings which, in a particular case, do not exhibit any need for compliance with F1D6. Such buildings must be considered on a case-by-case basis. However, it is the responsibility of a building proponent to satisfy the appropriate authority that the exemption should apply.
F1D7
Damp-proofing of floors on the ground
2019: F1.10
F1D7
Damp-proofing of floors on the ground
2019: F1.10
NCC Blurbs
NCC Title
Damp-proofing of floors on the ground
NCC State
SA
NCC Variation Type
Replacement
NCC SPTC Current
Damp-proofing of floors on the ground
Building Classes
1a,1b,10a,10b,10c
To prevent water penetration of roofs which could cause unhealthy and dangerous conditions or loss of amenity for occupants or dampness and deterioration of building elements.
Damp must not rise from the ground
F1D7 covers floors resting on the ground. The aim is to prevent ground dampness causing:
- unhealthy and dangerous conditions or loss of amenity for occupants; or
- dampness and deterioration of building elements (which, in this case, includes surfaces and linings inside the building, such as floor tiles, wall paint and the like).
Vapour barriers — AS 2870
AS 2870 is referenced for acceptable materials and installation details for vapour barriers to stop ground moisture reaching the upper surface of floors and walls.
Exemptions — F1D7(2)
Exemptions apply to F1D7 where:
- weatherproofing is not required for Class 7 or Class 8 buildings where there is no necessity for compliance, sheds forming part of a building used for other purposes, and so on (see the Limitations to F3P1 for a listing of exempted buildings); and
- the base of a stairwayor lift or similar shaftis suitably drained.
Figure F1D7 illustrates a method of installing damp-proofing in subfloor structures.
Figure F1D7: Installation of DPC in subfloor structures
Image
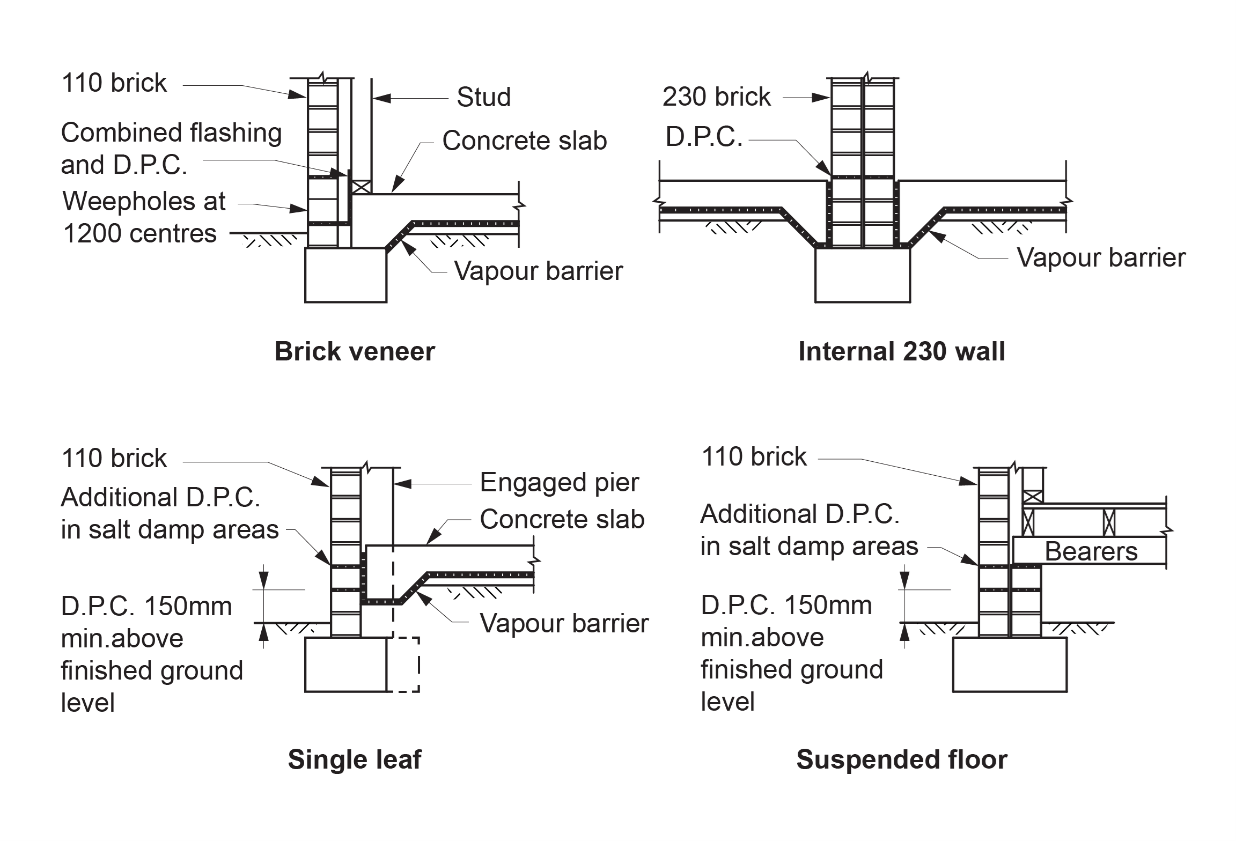
F1D8
Subfloor ventilation
2019: F1.12
F1D8
Subfloor ventilation
2019: F1.12
- be provided with openings in external walls and internal subfloor walls in accordance with Table F1D8 for the climatic zones given in Figure F1D8; and
- have clearance between the ground surface and the underside of the lowest horizontal member in the subfloor in accordance with Table F1D8.
- be cleared of all building debris and vegetation; and
- have the ground beneath the suspended floor graded to prevent surface water ponding under the building; and
- contain no dead air spaces; and
- have openings evenly spaced as far as practicable; and
- have openings placed not more than 600 mm in from corners.
- the subfloor ventilation required in (1) must be increased by 50%; or
- the ground within the subfloor space must be sealed with an impervious membrane; or
- subfloor framing must be—
- where above ground, above-ground durability Class 1 or 2 timbers or H3 preservative treated timbers in accordance with AS 1684.2, AS 1684.3 or AS 1684.4; or
- where in ground, in-ground durability Class 1 or 2 timbers or H5 preservative treated timbers in accordance with AS 1684.2, AS 1684.3 or AS 1684.4; or
- steel in accordance with NASH Standard ‘Residential and Low-Rise Steel Framing’ Part 2.
Climatic zone (see Figure F1D8) | Minimum aggregate subfloor ventilation openings without a membrane (mm2/m of wall) | Minimum aggregate subfloor ventilation openings having the ground sealed with an impervious membrane (mm2/m of wall) | Minimum ground clearance height where termite inspection or management system is not required (mm) | Minimum ground clearance height where termite inspection is required (mm) Note 1 |
---|---|---|---|---|
A | 2000 | 1000 | 150 | 400 |
B | 4000 | 2000 | 150 | 400 |
C | 6000 | 3000 | 150 | 400 |
Table Notes
- 400 mm clearance required only where termite management systems are installed that need to be inspected (see B1D4).
- On sloping sites, the 400 mm clearance required by (1) may be reduced to 150 mm within 2 m of external walls.
- In situations where openings in external walls and internal subfloor walls are not able to be provided, additional measures must be provided to ensure that the overall level of ventilation of the subfloor space is maintained.
- Additional measures referred to in (3) may include measures similar to those in F1D8(5), such as providing durability class timbers, or having the ground sealed in the subfloor space with an impervious membrane.
Figure Notes
The season with the highest relative humidity is used. Generally this will be July for southern Australia and January for northern Australia.
To prevent water penetration of roofs which could cause unhealthy and dangerous conditions or loss of amenity for occupants or dampness and deterioration of building elements.
Subfloor ventilation is cross ventilation of the subfloor space between the underside of the floor and ground surface under the lowest suspended floor of a building.
Ground moisture rising into or entering the subfloor space can create a damp environment which encourages timber rot, fungus growth and the potential for termite activity. Subfloor ventilation increases air flow, reducing any damaging water vapour in the subfloor space.
Factors that can affect achieving satisfactory levels of subfloor ventilation include height above ground, prevailing breezes (air transfer), differential temperature and humidity between the subfloor and the external environment and good building practice.
The amount of subfloor ventilation required for a building is related to the relative humidity likely to be encountered in that location. For the purposes of the Deemed-to-Satisfy Provisions, Australia has been divided into three broad climatic zones based on the prevailing relative humidity.
The climatic zones were determined by analysis of the average relative humidity at 9 am and 3 pm in January and July. The season with the highest relative humidity is used. Generally, this is July for southern Australia and January for northern Australia. The climatic zone limits are described in Figure F1D8.
Table F1D8 specifies the minimum amount of subfloor ventilation openings and height of subfloor framing members above ground level for the three climatic zones illustrated in Figure F1D8. The table allows subfloor ventilation rates to be halved if the ground within the subfloor space is sealed by an impervious membrane because humidity levels in the space will not be affected by moisture from the soil.
F1D8(5) specifies additional requirements for preventing deterioration of subfloor members where the ground or sub- floor space is excessively damp, as would occur in areas with high water tables, poor drainage or in areas frequently affected by flooding or water inundation.